Piaget The Endless Yet Thinnest Journey
When we describe something very thin, we would say “as thin as a rake”. But perhaps we could also say it in this way, “as thin as Piaget’s watches”. Every year Piaget presents us with its ultra-thin watches and goes on with even slimmer successors. Will the Altiplano 900P be a finale? During this year’s W&W, their CEO humbly implied the journey would probably come to an end. But we just think they will anew stun the world for sure. Before 2014, who else can think of using the caseback as mainplate and create a mechanic watch with a thickness of only 3.65mm? Piaget seemingly never stops expanding its expertise in thin movements.
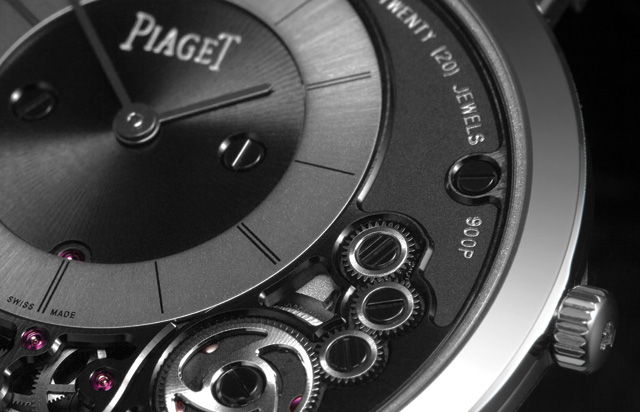
Ultra thin – A Lifelong Legacy
Ultra-thin timepieces and the name Piaget have gone hand in hand for many decades. Half a century earlier, they have been producing scores of very thin movements. These ultra-thin watches not only have simple functions, but also marry with complicated functions like minute repeater, perpetual calendar and tourbillon.
In retrospect, the development of thin movement has gone through three stages. The expertise goes all the way back to 1957 with the invention of the 2mm thick 9P movement, even slimmer than some crystal glass. And in 1960 they created the 12P automatic movement measuring only 2.3mm thick, followed by the 430P hand-wound movement at 2.1mm thick. This famed movement offers numerous possibilities in terms of variations and serves as the model for the 450P movement with small seconds and the world’s thinnest shaped tourbillon movement 600P. Since the debut of the 2.35mm thick automatic movement 1200P in 2010, the Manufacture has presented us ultra-thin movements every year and beaten its own record to produce the world’s thinnest movement, contributing a line-up of minute repeater, tourbillon and skeleton models.
Piaget has created 37 in-house movement so far and 25 of them are ultra-thin movements, among which 14 set the new records. Over the past four years, the 1200P automatic movement has played a key role in various categories. Yet, the 900P, star of this year, can’t earn the thinnest movement title but the world’s thinnest mechanical watch – with the case and movement merging into one.
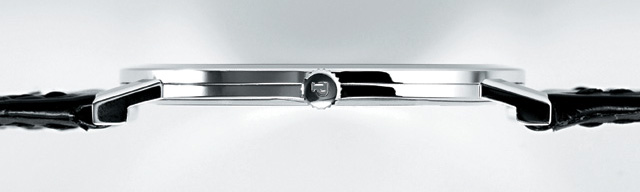
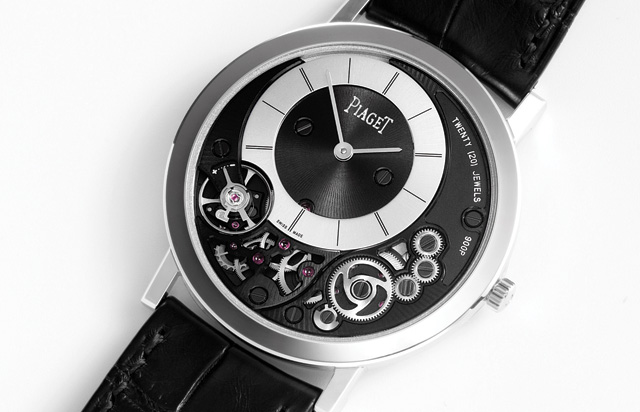
Altiplano 900P
Ultra-Thin – All about Fierce Determination
In speaking of ultra-thin watches, the thickness of movement is the crux of the watches. But it’s not the case in Altiplano 900P. Because its case is now directly integrated into the movement. The case and movement become a single entity. With its admirable 3.65mm height, the Altiplano 900P is now the world’s thinnest mechanical watch.
Innovations in watchmaking come in different ways. Bold apertures are designed for clear legibility, silicon parts for anti-magnetic and anti-rusting purposes. This year Piaget has taken some serious technological breakthroughs to bring us the Altiplano 900P that sits comfortably on wrist. These days, many brands produce in-house movements, while some specialised in cases. Only can a handful of brands produce both in-house movements and cases. Piaget is no doubt one of these first-tier manufactures. The Altiplano 900P displays an astonishing feat of movement engineering and case design, showing the amazingly thin silhouette of the piece. Besides demonstrating the aesthetic slim contour, every component is optimally fixed to ensure smooth running of the mechanism.
The case of Altiplano 900P serves as the mainplate for the movement. The parts are directly embedded on the case while space is freed from the original mainplate. Additionally, the off-centre dial is assigned into the same layer with the plates, aiming to further reduce the thickness of the case. There are 145 movement components in all, each are trimmed down as much as it can be. Some of the wheels of the main gear train come in at only 0.12mm thin. To give life to this stunning piece, the Manufacture spent a full three years on the development. Incredibly thin, the piece is made of traditional materials instead of aeroplane or medical composites. Sounds more adorable?
Apart from the trimmed components, Piaget takes an entirely new approach upon the construction of the piece. Since the flat crystal glass sits as close as the movement, it would press on the hands when subjected to pressure. To solve this, Piaget has placed the hands underneath the bridges. In case of the effects of pressure, the crystal glass would press not on the hands but instead on the wheel-train bridge, thus avoiding any consequences on the rate of the movement.
For the movement is surfaced on the dial, every part has been meticulously polished, while the bridges are black-coated to create elegant contrasts with the fan-shaped balance-wheel and the entirely wheel-train system in the bottom.
Powered by a hand-wound movement, the piece is sized at 38mm with 48-hour power reserve. The piece is available in white gold, rose gold, white gold with diamond-set bezel, as well as a high jewellery version with baguette-cut diamonds, 38 on bezel and 33 on dial. Last but no least, it should be mentioned that the 38mm case is truly praiseworthy. If a 40mm case were used, it wound still be in line with the current trend of watch size and need less efforts to allocate the parts to reduce the case thickness. Nevertheless, Piaget decides to stick at 38mm and takes its engineering to new heights.
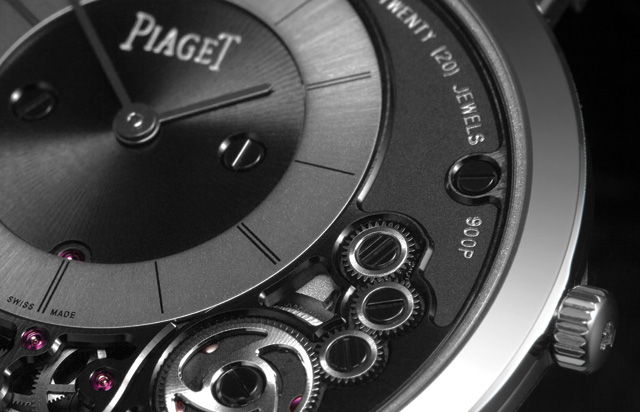
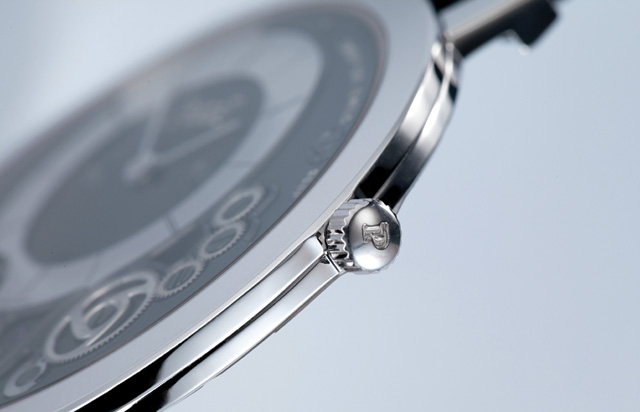
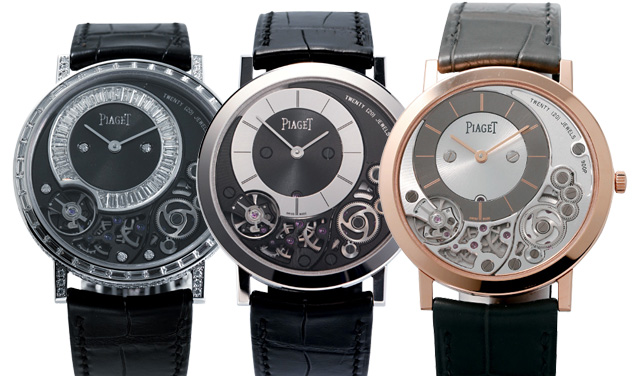
Altiplano Skeleton Enamel
Ultra-thin – Make Peace With Enamel
The name Altiplano is the bywords of Piaget’s 50 years of ultra-thin journey. In the 1990s, the Manufacture created the ultra-thin 430P movement and first put it in the Altiplano collection. Later in 2010, the 1200P movement was again housed in the Altipano watch to celebrate the 50th anniversary of the legendary 12P movement. The reason is clear: the minimalist Altiplano is perfectly matched with the sleek silhouette of ultra-thin movements.
Among Piaget’s 25 ultra-thin movements, 5 are skeletonised. The very first skeleton movement 9S was released in the 1970s, while the 600S movement awarded the world’s thinnest skeleton tourbillon hand-wound movement, not to mention the world’s thinnest skeleton automatic movement 1200S. And this year, two new variations debuted, namely the 1200E and 1200G.
Based on the 1200P movement, the 1200S skeleton movement at 2.4mm thick already required much effort to create. This year, the Manufacture introduced its first ever enamelled skeleton movement 1200E. The “E” probably stands for extra efforts. Indeed, Blancpain once made an inverted movement with enamel on the plates, but Piaget this time transposed the enamel on the skeletonised mainplate which is incredibly difficult in doing so. First, the special enamel is composed of pure silica and metal oxides. The artisan then coats five layers of enamel on the mainplate. When each layer is done, it will undergo firing at temperatures between 780 and 800 degrees Celsius. In order to achieve the glossy appearance and avoid any risk of distortion, the Manufacture spent 2 years of development, including an entire year for the enamel issue alone, to invent this avant-garde creation – an enamelled skeleton movement.
This timepiece follows the Altiplano tradition with a diameter of 38mm. Since the mainplate is enamelled and set with 11 black or red black sapphire cabochons, the 1200E movement is 0.6mm thicker than the 1200S movement. Yet, its 3mm thickness still claims the crown for the world’s thinnest skeleton enamel automatic movement. The piece is available in 2 versions: white gold case with black enamel or rose gold case with white enamel. The latter is adorned with a diamond-set bezel, offing a choice of couple watch.
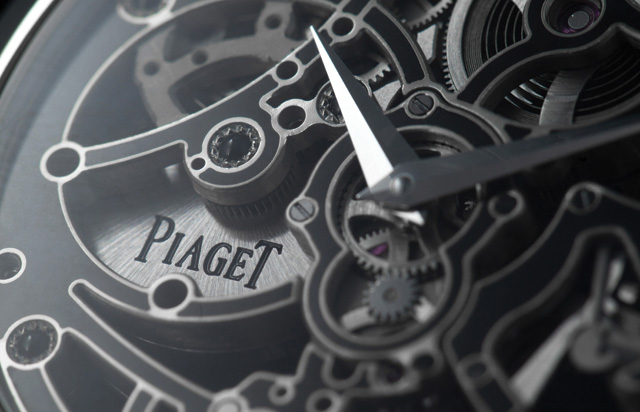
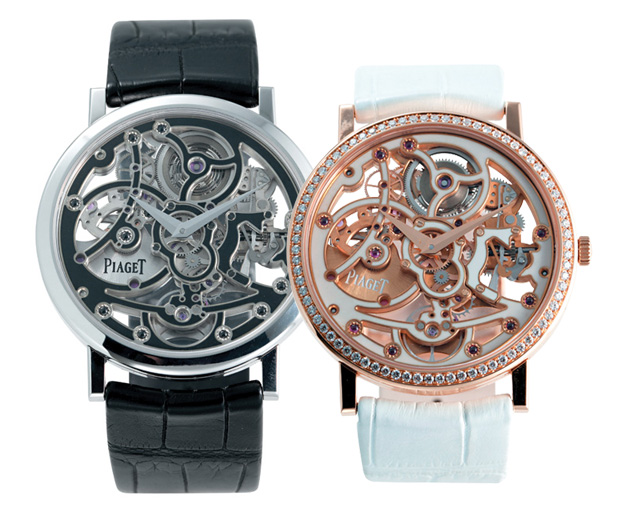
Making of Skeleton Enamel
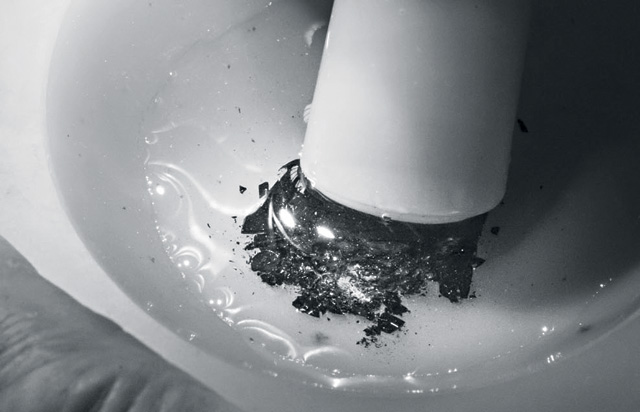
1. The artisan first grinds the special enamel with water. This special enamel can withstand the same traction as the skeletonised 18K gold mainplate, so it would not be distorted in the firing.
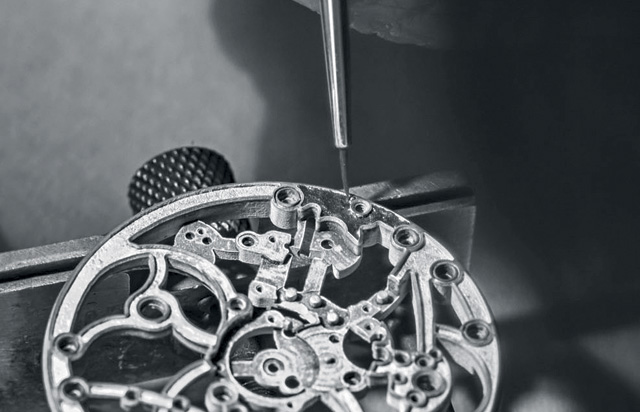
2. The enamel is applied meticulously on such a thin plate.
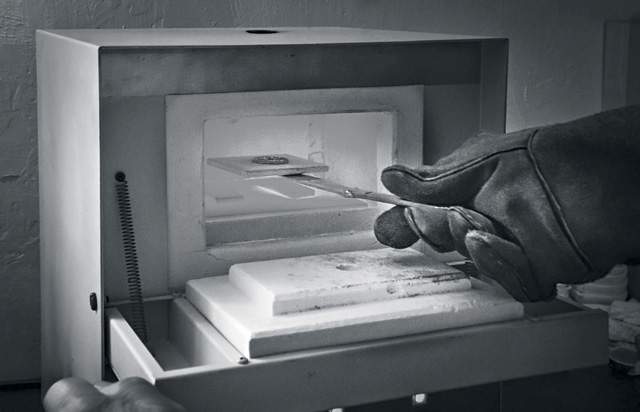
3. The enamel undergoes five successive firings at temperatures between 780 and 800oc degrees Celsius.
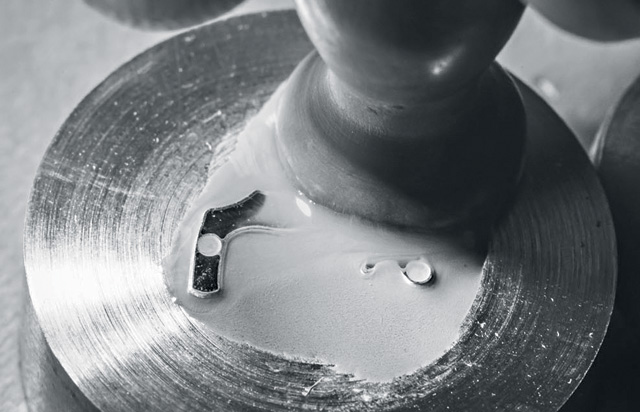
4. The movement is hand-polished so as to give the enamel a shining surface.
Altiplano Skeleton Engraved
Ultra-thin – Make Peace With Engraving
Piaget has, in its roots, the mastery of creating ultra-thin movements and upholds the endless quest in making them. The ultra-thin 1200P movement has evolved to offer skeleton models featuring enameling and engraving. One day, perhaps, we would see the micro-mosaic or embroidery technique applying on skeleton dial.
The 1200G movement measures 2.4mm thick, same as the 1200S skeleton movement. Most skeleton movement’s components are trimmed down as much as it can. An engraved skeleton dial, however, leaves optimal space for engraver’s expression. The 1200E movement adds enamel on bridges and undergoes several firings, which create a certain risk of damaging the whole dial. The making of 1200G movement is like skating on thin ice as it also needs meticulous care to do the engraving without affecting the smooth running of the movement.
The Intaglio Engraving art is applied on this beautiful piece. It aptly adds a sense of depth on the 14K rose gold coated mainplate and bridges. This craftsmanship is commonly seen in A. Lange & Soehne’s engraved movement to give a pretty awesome look. The Manufacture chooses also this refined artistry to create its first engraved ultra-thin skeleton movement. The 38mm case is made in rose gold, echoed the 14K rose gold mainplate.
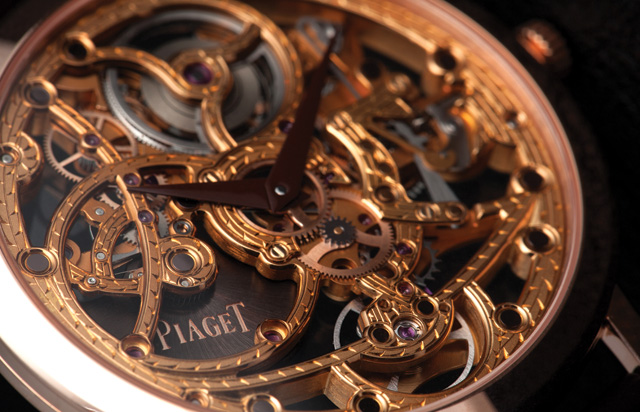
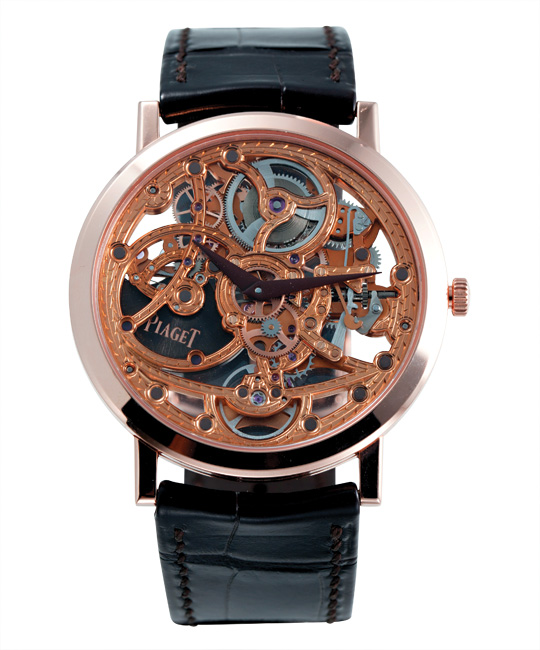
Making of Skeleton Engraving
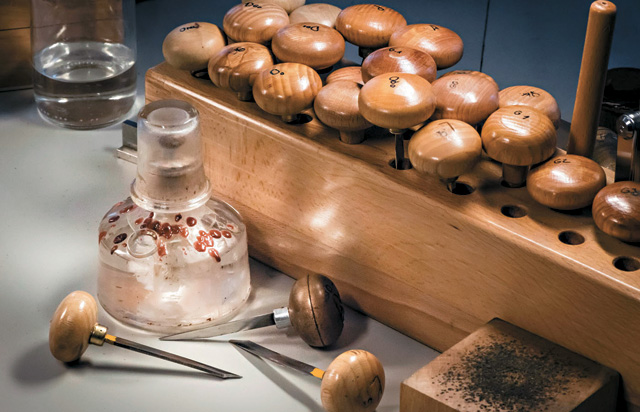
1. Artisans use engraving tools of various sizes to correspond different situations.
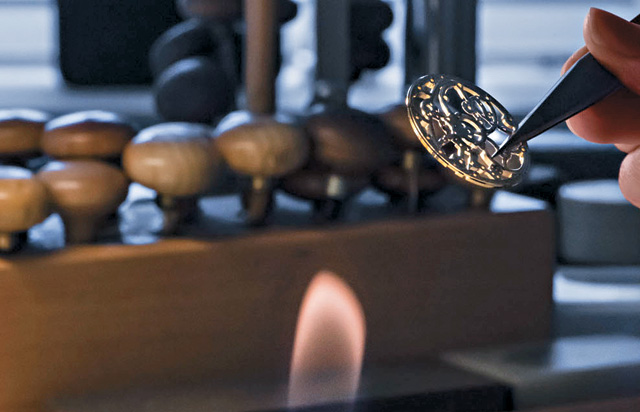
The skeleton movement is heated before cementing on the carving base.
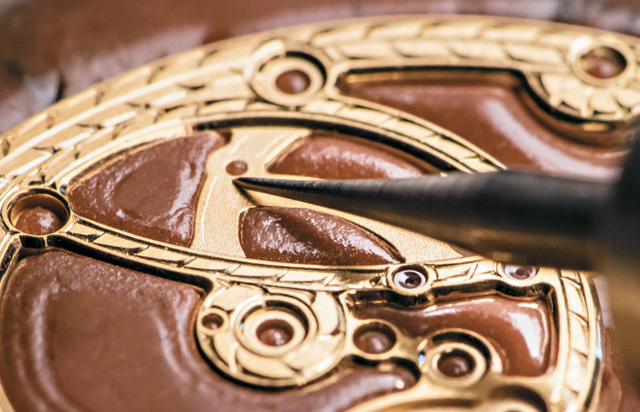
Start engraving the 1200G movement. This is a real challenge to engrave on a skeleton dial.
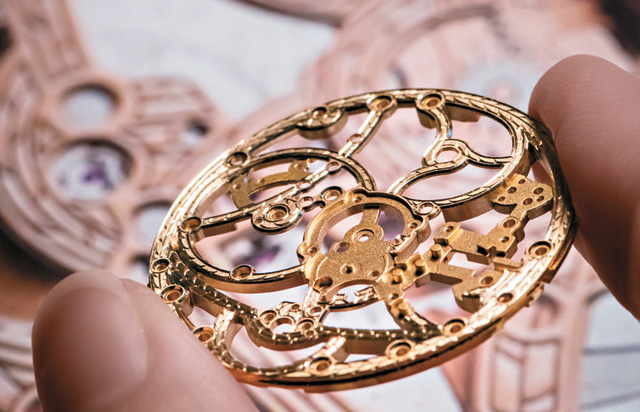
4. Compare the 1200G movement with the gouache painting to make sure it’s perfectly precise.
Metiers d’Art Altiplano Scrimshaw Engraving
Ultra Thin – A Perfect Companion With Elegance
The canvas-like dial is in fact made by an age-old craftsmanship called scrimshaw engraving. This needle-type engraving technique was born in the 18th century while the whalers used whale or walrus teeth as a medium for the engraving. For people today cherish endangered species, fossilised mammoth teeth has thus replaced ivory and whale’s teeth; yet, the spirit of this art remains unchanged. This form of expertise requires the artisan to do the engraving from dots to lines and finally form the shape of the globe. After that, the artisan brings the motif to life by applying ink that accentuating the contrasts. A traditional world map dial are usually involved enamel. Albeit the scrimshaw engraving is not vibrant as enamel painting, it showcases exceptional vigor and beauty. To finish one dial, the scrimshaw engraving master Richard Maier spends no less than 65 hours of work. Two versions are on offer: white gold and rose gold, each limited to 88 pieces. Personally speaking, the rose gold case looks more harmonious with the watch’s map theme.
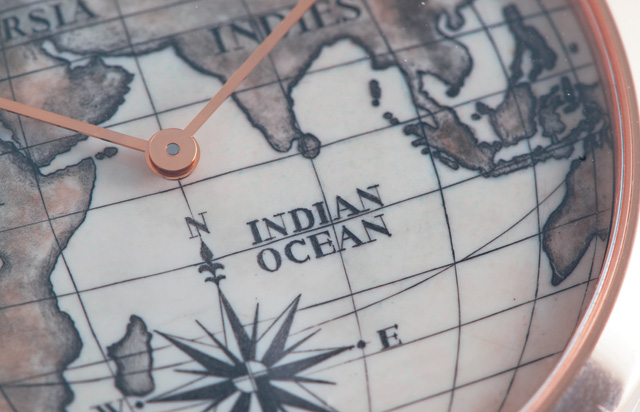
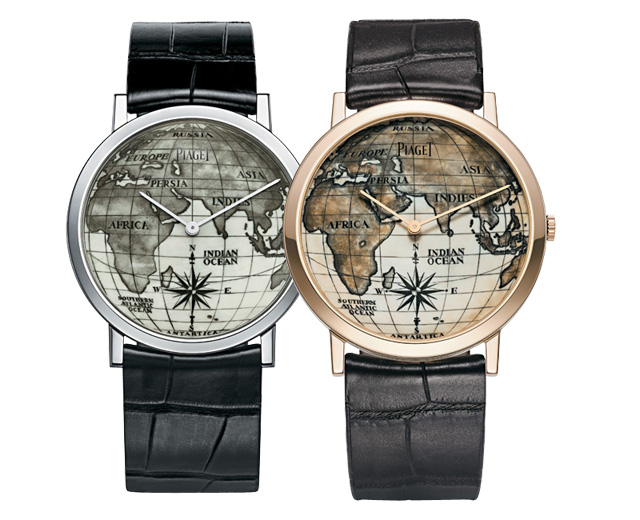
Metiers d’Art Altiplano Bullino Engraving
And this painting-like horse motif was actually crafted by the bullino technique from Italy. The engraving is done through a whole series of lines and dots by just a fine metal needle and tip. To engrave the contour of the horse, a metal needle is first used to perform the engraving on the dial, after which the shiny parts of the animal are done by using the bullino technique. The part of the horse in grey is bullino-engraved at a 90° angle, whereas the section that must be much darker is done at an 80° angle. You can admire the gradation of brightness and texture by examining the horse’s mane and black mouth. As if that weren’t enough, the motif is applied an oxidising product to lend a touch of colour and polished with wooden pegs and a polishing paste that adds brilliance. A last layer of black colour is then applied to the whole, thus forming this masterpiece with a total production of only 18 rarities.

Rose Passion Altiplano
Named after Yves Piaget, the fourth generation of Piaget, the Yves Piaget Rose collection exhibits various forms of this vibrant flower. We’ve seen a micro-mosaic and embroidery rose before. Now we would like to show you one created by a traditional craftsmanship. The cloisonne enamel dial of this stunning piece is crafted by the Grand Feu technique. The Artisan first outlines the desired decorative pattern by silver or gold wire and marks off a certain number of hollows. Once the design has been reproduced, the enamel is then deposited in each of the hollows and fixed with tracaganth gum that will disappear during the firing process. The enamel painting is finished after several times of firing. The micro-mosaic or embroidery technique lends a lifelike quality to the rose while this rose in cloisonne enamel is much like a real painting. The tiny “AP” signature painted on the bottom of the dial tells it is again a creation by Anita Porchet, an internationally-acclaimed enameller.
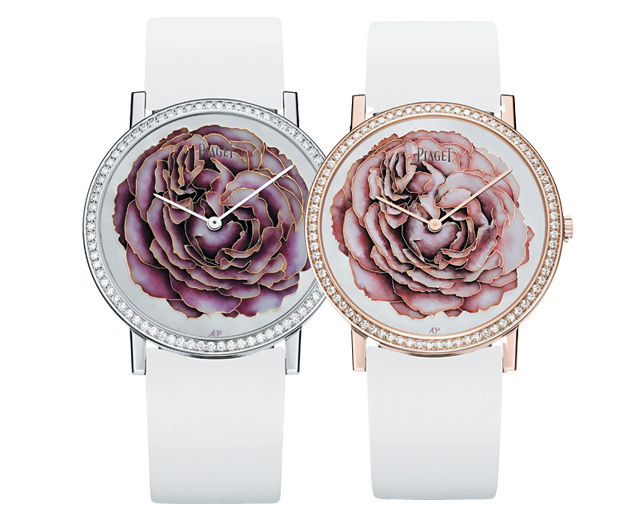